Emulsifying Machine
SINDA is a professional manufacturer of Emulsifying Machine. ZJR Series Vacuum Emulsifying Machine is a specialized equipment for producing medicinal ointments, high-grade creams, lotions, and more.
What Parts Does a ZJR Series Vacuum Emulsifying Machine Consist of?
ZJR Series Vacuum Emulsifying Machine is composed of frame, homogenizing mixing pot, lifting and flipping mechanism, homogenizing mixing mechanism, water pot, oil pot, vacuum system, temperature control system and Electrical control.
Working Principle of ZJR Series Vacuum Emulsifying Machine
ZJR Series Vacuum Emulsifying Machine achieves efficient and uniform emulsification by Removing air through a vacuum, Stirring mixed materials, Shearing and refining particles and Ensuring uniform dispersion through circulating flow.
It uses vacuum, stirring, shearing, and other actions to mix two or more immiscible liquids (such as water and oil) into a stable emulsion.
Circular Flow: The high-speed rotating stator and rotor generate strong circulation in the emulsification pot. Centrifugal force accelerates and throws material outward, colliding with the stator for further dispersion and homogenization. This ensures the material reaches an ideal emulsified state quickly.
Vacuum Action: The vacuum system generates negative pressure through a vacuum pump, drawing air out of the emulsifying pot to form a vacuum state. This reduces bubbles, prevents oxidation, maintains product stability, and extends shelf life. The vacuum state also improves emulsification, as particles of the dispersed phase are more easily dispersed evenly in the continuous phase.
Stirring and Homogenization: The emulsifier is equipped with high-speed rotating agitators and scrapers, producing strong shearing and frictional forces. The agitator design causes vortex flow in the emulsification pot, ensuring thorough mixing. The scraper continuously scrapes material off the pot wall to avoid dead spots caused by adhesion.
Shearing Action: The homogenizer, the core component, consists of a high-speed rotating cutting wheel and a fixed cutting sleeve. As material passes through the narrow gap between the cutting wheel and sleeve, it undergoes strong shearing and impact, refining dispersed phase particles to 200nm to 2µm, forming a stable emulsion.
Does ZJR Series Vacuum Emulsifying Machine Unit Need a Water Pot and an Oil Pot?
The auxiliary machine of ZJR Series Vacuum Emulsifying Machine unit usually includes a water pot and an oil pot. While these are optional, they are essential for certain processes:
Heating and Dispersing:Equipped with heating and dispersing functions, they pre-treat materials by dissolving, dispersing, heating, and stirring.
Water and Oil Pot Separation: They can separate water phase material from oil phase material.
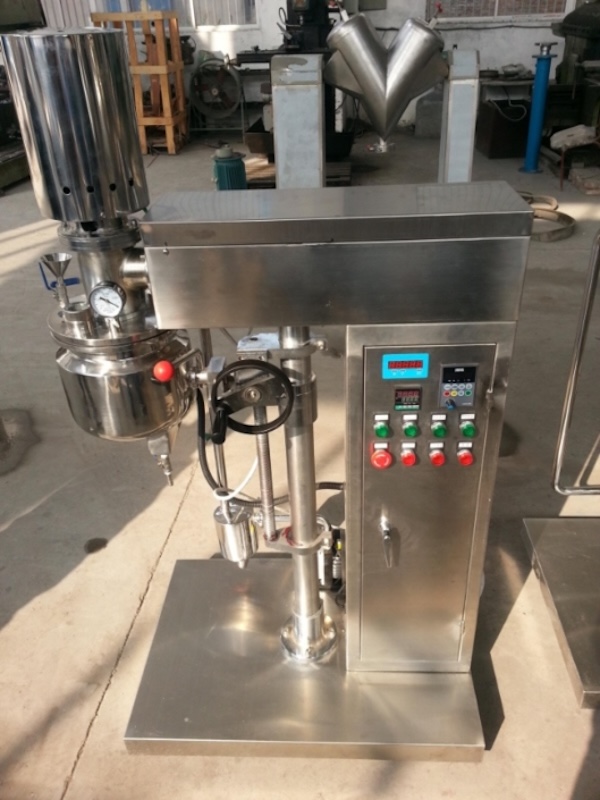
Does ZJR Series Vacuum Emulsifying Machine Unit Need a Water Pot and an Oil Pot?
The auxiliary machine of ZJR Series Vacuum Emulsifying Machine unit usually includes a water pot and an oil pot. While these are optional, they are essential for certain processes:
- Water and Oil Pot Separation: They can separate water phase material from oil phase material.
- Heating and Dispersing:Equipped with heating and dispersing functions, they pre-treat materials by dissolving, dispersing, heating, and stirring.
The Key Features of ZJR Series Vacuum Emulsifying Machine
ZJR series vacuum emulsifying machine is an efficient and multifunctional emulsification equipment, ideal for producing high-viscosity emulsions such as creams, ointments, and lotions.
– Automatic Lifting Pot Lid: Ensures materials enter the emulsifying pot without contamination under vacuum and facilitates material observation and processing.
– Vacuum Conveying System: Materials in the water and oil pots can directly enter the emulsification pot under vacuum, reducing oxidation and bubbles, and ensuring product quality and stability.
– Discharging Method: Offers multiple discharging methods, such as pot flipping and bottom valve discharging, for convenient and fast product removal while reducing contamination.
– Temperature Control System: The heat-conducting medium in the pot’s interlayer is heated by an electric heating tube for precise heating, with the ability to set and automatically control the temperature. Cooling can also be done using coolant in the interlayer.
– Efficient Mixing and Homogenizing System: Can operate separately or simultaneously, completing micronization, emulsification, mixing, and dispersion in a short time, ensuring product gloss and stability.
– Hygiene and Safety Design: Made of high-quality stainless steel (SS304 for general use, SS316L for pharmaceutical use), with a mirror-polished inner surface to ensure hygiene. The design complies with GMP specifications and features a unique integrated sight glass and enclosed lighting for material observation. The triple-jacket structure and aluminum silicate insulation ensure operational safety and efficiency.
– Diverse Interface Configurations: Equipped with various quick-installation interfaces, such as sterile air respirators, material suction inlets, vacuum pump interfaces, cleaning balls, CPI interfaces, trace element adding inlets, integrated sight glass windows, and vacuum meters, enhancing adaptability and convenience.