Blister Packaging Machine
SINDA is a professional manufacturer of blister packaging machines. BPM series blister packaging machines, developed from roller-type machines, utilize plate-type heating, forming, filling, heat sealing, and cutting processes. They cater to a wide range of applications, including the packaging of tablets, capsules, softgels, injectables, and various medical devices. The machines are versatile, accommodating different shapes and sizes of products, including round, square, triangular, oval, and elliptical forms. They can also package ampoules, vials, and larger or more sensitive medical devices.
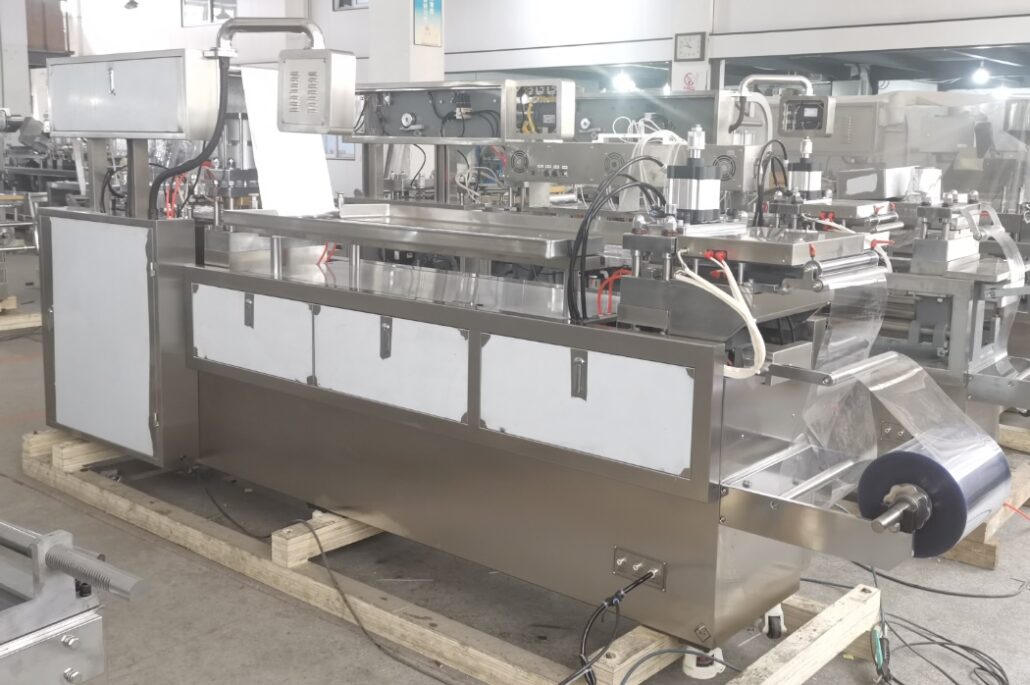
Working Principle and Components of BPM Series Blister Packaging Machine
BPM series blister packaging machines heat the forming film with a plate-type heater to soften it. The softened film is then blow-molded into blisters using compressed air. The filling section fills these blisters, which are then sealed with a covering film in the sealing section. Batch numbers and indentation lines are printed, and the final products are cut to size.
Heating Section:
– Direct Heating: Heats plastic sheets by direct contact with the heater. This method is rapid but uneven, making it suitable for thinner materials.
– Indirect Heating: Uses radiant heat to evenly and thoroughly heat the plastic sheets, suitable for both thick and thin materials despite its slower speed.
Forming Section:
– Compression Molding: Utilizes compressed air to press softened sheets against molds, fitting them tightly against the mold walls to form blisters. This method is suitable for both deep and shallow blisters and typically uses flat-plate molds that can operate intermittently or continuously.
– Vacuum Forming: Employs vacuum suction to adhere softened sheets to the mold’s surface, forming blisters. It is suitable for shallower blisters and thinner materials, generally using rolling molds with continuous transmission.
Filling Section:
– Quantitatively fills the formed blisters with medication using various feeding systems, such as brush feeders and multi-row automatic fillers.
Printing and Indentation Section:
– Prints batch numbers on the medicine boards using steel characters and creates indentations to facilitate folding.
Cutting Section:
– Cuts the packaged products into the desired sizes.
Video of Blister Packaging Machine
Differentiation of BPM Series Models
- BPM-A: Button-controlled model.
- BPM-C: Touchscreen-controlled model.
- Numerical Suffix: Indicates the maximum width of the standard equipment’s film (e.g., BPM-250C has a maximum film width of 250mm).
Advantages and Features of BPM Series Blister Packaging Machine
- Advanced Control System: Utilizes branded PLC systems with touchscreen interfaces for intuitive operation. BPM-120A is button-controlled, while BPM-120C combines PLC and touchscreen control.
- Traction Options: BPM-120 uses mechanical traction, while other models offer both mechanical and servo motor traction options.
- Safety Features: Equipped with overload protection to ensure high safety performance.
- Custom Feeders: Provides specific feeders for different products to ensure safe and complete packaging.
- Stable Operation: Employs special processing and assembly techniques to ensure the stable operation of the packaging film.
- Waste Collection: Features an automatic waste collection mechanism that ensures uniform collection and orderly output of finished products.
- Versatility: Capable of producing both aluminum/aluminum and aluminum/plastic blisters with interchangeable molds.
- Adjustable Components: Allows adjustment of forming, heat sealing, and cutting parts along the machine’s guide rail to accommodate various blister sizes with high precision and versatility.
Considerations for Purchasing BPM Series Blister Packaging Machine
- Material Compatibility: Determine if the machine will be used for aluminum/PVC or aluminum/aluminum blisters, or both, as this requires different molds and feeders.
- Material Width: Select a model based on the width of the packaging material (e.g., BPM-250C for a 250mm wide material).
- Product Specifications: Provide specifications and dimensions of the product to be packaged.
- Integration with Other Equipment: Inform if the blister packing machine needs to connect with other production equipment (e.g., cartoning machines).
- Power Requirements: Specify the workshop voltage to ensure compatibility.
- Compressed Air: Requires compressed air with a working pressure of 0.60MPa and a consumption of at least 400L/min.
- Cooling Requirements: Usually requires cooling water for operation; optional chiller provision if needed.
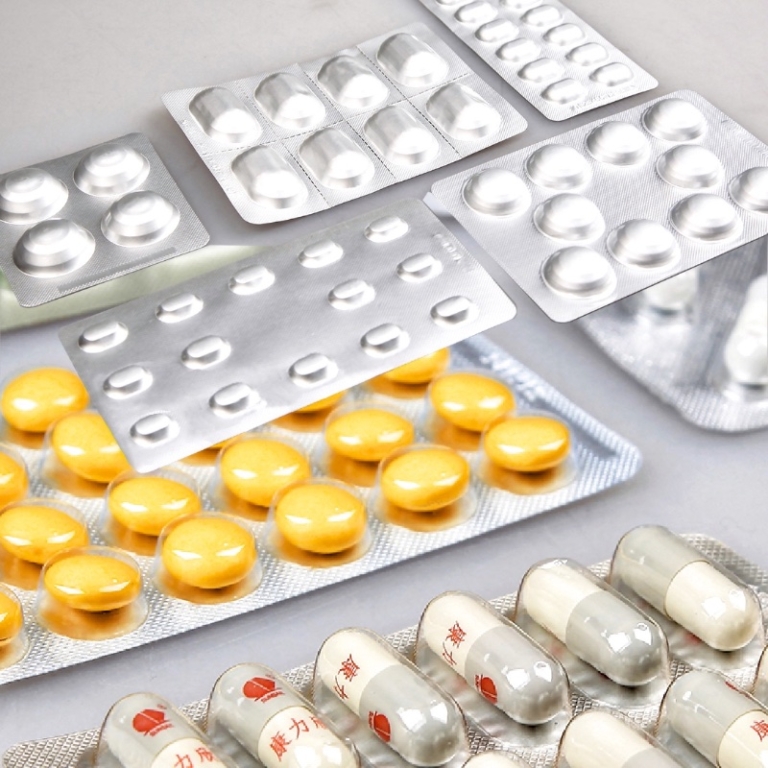
Applicable Packaging Materials
– Aluminum/Plastic Blisters: Made from rigid plastic sheets (PVC/PVDC/PE, PVDC/OPP/PE, PVC/PE) and coated aluminum foil.
– Aluminum/Aluminum Blisters: Made from cold-formed aluminum and coated aluminum foil.
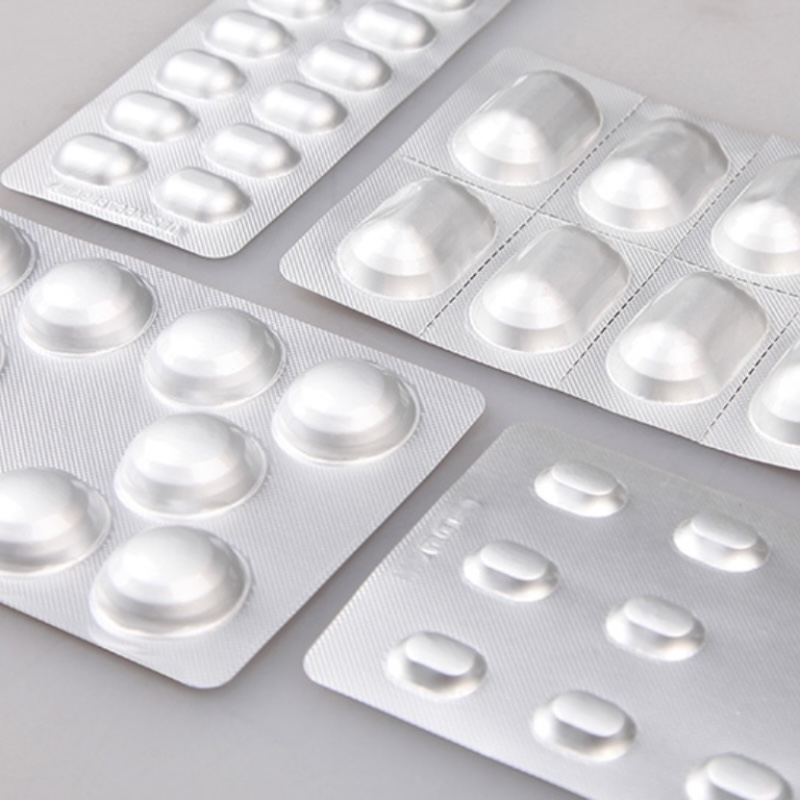
Blister Packaging Production Line
Blister packaging machines can be integrated with cartoning machines to form a complete automated blister packaging production line. This setup is ideal for large-scale production with fixed varieties, ensuring safety and hygiene.
Video of Blister Packaging Line