Granulator Machine
Sinda is a professional supplier of granulator machines. They are widely used in pharmaceutical, chemical, food and other industries. They are used to process powdery materials into granules with a certain shape and size. According to the different working principles and structural characteristics, granulator machines can be divided into YK series wet granulator machine and SHK series high-speed mixing granulator machine.
YK Series Wet Granulator Machine
YK series wet granulator machine mainly produces granules by using the rotating drum to press wet powder materials through a screen. It can also granulate crushed and compacted materials.
In the chemical and pharmaceutical industries, it can make wet powder into granules, then dry it to press it to tablets. Additionally, it can crush materials that have caked during storage. However, it is not suitable for granulating semi-solid, liquid, or paste materials.
Features of YK Series Wet Granulator Machine
YK series wet granulator machine is sturdy, it is easy to operate and runs smoothly. It has a large volume hopper. The rotating drum is made of stainless steel.
The mesh size of the screen can be customized according to the required granule size. The screen is clamped by two steel tubes, making installation and removal simple. The tension is supported by fine-toothed gears and can be adjusted accordingly.
Structure of YK Series Wet Granulator Machine
YK series has an independent rectangular structure with a sealed bearing seat connected to the hopper. The hopper extends outside the rectangular structure, under the hopper, it is a steady base, providing a wide and stable ground contact. No installation is needed, and it can be placed indoors for use.
The granulation device features a rotating drum that lies horizontally beneath the hopper, with bearings at both ends. It moves back and forth via rack transmission. The front end bearing cover is removable. Loosening three wing nuts allows the rotating drum to be pulled out. Both ends of the rotating drum have protruding square rings embedded in the bearing seat to prevent oil contamination in the powder.
The gearbox uses worm gear transmission, with a speed ratio of 1:12. The box stores machine oil to ensure proper gear lubrication and quiet operation. There is a sight glass to observe the operation and oil level. The worm gear shaft’s outer end drives the eccentric shaft, which moves the rack back and forth.
The screen clamp is located on both sides of the rotating drum. It is made of steel pipes with a long slot in the middle. Both ends of the screen are embedded in the slot. Turning the flower-shaped handwheel wraps the screen around the rotating drum. The handwheel has gears inside to adjust tension.
The motor mount is fastened with screws, and the motor is placed on an iron plate. Turning the screw can adjust the motor’s height.
Video of YK Series Wet Granulator Machine
Instructions for Use
1. Start the machine and pour the mixed material into the hopper. Under the oscillation of the rotating drum, the material is granulated through the screen and collected. For crushing block materials, add them gradually to avoid damaging the screen.
2. If powder stays in the hopper and doesn’t move, do not use your hands to clear it. Use a bamboo stick or stop the machine to prevent injury.
3. Choose the speed based on the material’s viscosity and moisture content. Dry materials can run faster, while wet materials should run slower. The exact speed range can be determined through practical operation.
Lubrication of YK Series Wet Granulator Machine
All rotating parts of the machine have oil cups, which should be filled with grease or oil before starting the machine. Add oil midway based on bearing temperature and operation.
The worm gear box should always contain oil, with the oil level high enough to submerge the worm gear. If the machine is used frequently, change the oil every three months. There is a drain plug at the bottom for oil drainage.
Avoid overfilling the oil cups and prevent oil from spilling onto the machine or floor, which could contaminate the materials and affect product quality.
Maintenance Instructions
Regularly check the machine parts, once a month, to ensure the worm gear, worm shaft, bearings, and other moving parts are functioning smoothly and not worn. Fix defects promptly and avoid forced operation.
The machine should be used in a dry, clean indoor environment and not in areas with corrosive gases like acids.
After each use or downtime, remove the rotating drum for cleaning and clear any remaining powder from the hopper. Reassemble the machine for the next use.
If the machine will be unused for a long time, clean it thoroughly. Apply anti-rust oil to exposed parts and cover the machine with cloth for protection.
SHK Series High-speed Mixing Granulator Machine
SHK series high-efficiency mixing granulator machine completes mixing and granulation in one step. It has high production efficiency and excellent granulation results. It complies with GMP standards.
SHK series integrates light, electricity, and gas. It uses Siemens PLC control. The machine has a touch screen display and stepless frequency conversion speed regulation. It features an innovative adhesive dosing device with a dripping method. It has an automatic safety protection system, jacket heating, and temperature control. SHK series is fully functional and highly automated. It can mix and granulate powders and pastes into uniformly sized particles. SHK series is suitable for industries such as pharmaceuticals, food, chemicals, and metallurgy. It is particularly useful for mixing and granulating traditional Chinese medicine extracts and powders.
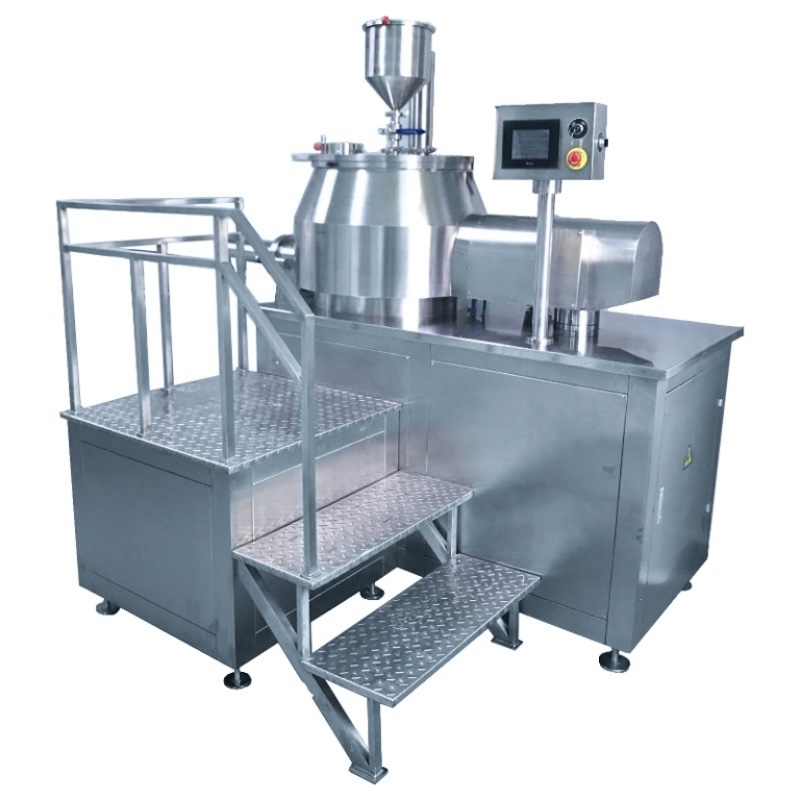
Performance Features of SHK Series High-speed Mixing Granulator Machine
- SHK series uses PLC control with a human-machine interface display. Temperature, run time, speed and formulas can be input into the machine. It operates automatically and is easy to use.
- The cutting knife has a V-shaped blade in addition to the traditional straight handle. This blade shortens the granulation time. The unique stirring paddle helps scrape material from the container wall. It reduces material accumulation and improves granulation efficiency.
- The jacketed pot allows for heating or cooling as required. The temperature inside the container can be set.
- SHK series includes a dripping device. Adhesive can be added through dripping or directly. This device reduces adhesive use and the granulation results are excellent.
- The SHK series has a reliable safety protection system. When the lid is open, the main machine can only be started with a password. This system ensures the safety of both operators and machine.
- The pot lid has dust removal device and adhesive injection port. The granulation process can be monitored at different stages through the viewing port, achieving a dust-free operation.
- The seals of the cutting knife and stirring paddle shafts use a combination of rubber rings with oil and spiral pressurized air. The shaft seals are designed to be removable, making maintenance easy.
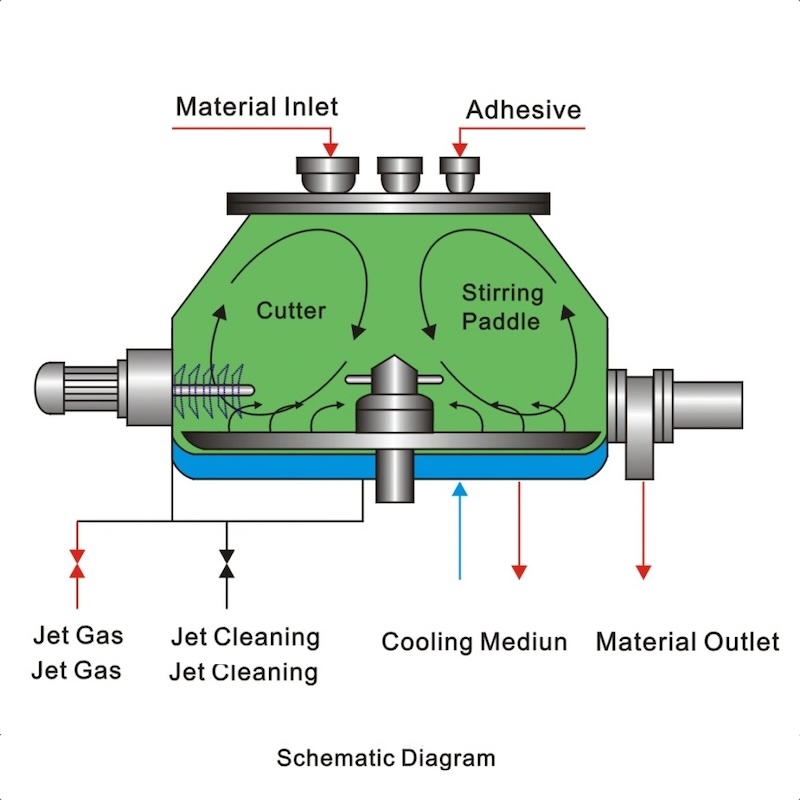
Working Principle of SHK Series High-speed Mixing Granulator Machine
SHK series consists of the frame, jacketed pot, pot lid, stirring paddle, cutting knife, discharge port, feeding device, flying knife transmission, stirring transmission, heating or cooling system, and an automatic control system.
The SHK series uses a jacketed pot as a material container. The stirring paddle and cutting knife rotate to provide power. After starting, the stirring paddle mixes the material at the set speed. Adhesive is added through the feeding device. The material is quickly mixed and granulated. The cutting knife then cuts the material into the desired granules. Finally, the discharge port opens, and the granules are automatically discharged. By adjusting the speed of the stirring paddle and cutting knife, granules of different sizes can be obtained.
Main Components
1. Frame: The frame of SHK series is welded from angle steel and plate steel and covered with stainless steel. It supports various components. Inside, it houses the stirring motor, stirring reducer, and pneumatic components that control the movement of the pot lid.
2. Stirring Mechanism and Jacketed Pot: The stirring mechanism is powered by a motor. The reducer’s output shaft is the stirring shaft. The stirring paddle is attached to the shaft. The jacketed pot is installed above the base plate. A detachable seal assembly is placed between the stirring shaft and the jacketed pot.
3. Cutting Mechanism: The cutting mechanism is powered by a motor. The cutting knife rotates at high speed inside the pot, cutting the material into granules. A sealing mechanism is placed between the cutting knife shaft and the motor base.
4. Pot Lid: The pot lid is made of stainless steel. A T-shaped silicone sealing ring is mounted at the bottom. The lid has observation, dripping, and exhaust holes.
5. Discharge Port: The discharge port is installed on an anti-rotation cylinder. When the cylinder pushes forward, clean air clears the discharge port, sealing the door. When the cylinder retracts, the discharge port opens, allowing granules to be automatically discharged.
6. Automatic Lifting Device for Stirring Paddle (Note: This is not available in models below SHK-100): A cylinder connects to a top rod, lifting the stirring paddle. This allows for thorough cleaning of the pot and easy observation of previously obstructed areas, solving the issue of hard-to-clean areas in the granulation pot.